High-Performance Polymer Extruders for Australia & NZ
Introduction
Plastic products power many industries, from packaging and construction to automotive and appliances. Behind each plastic pipe, film, or component is a polymer extrusion machine turning raw pellets into useful products.
For manufacturers and engineers in Australia, New Zealand, and the Pacific, choosing the right extrusion equipment is key to efficiency, product quality, and profitability. Whether you're extruding simple profiles or advanced polymer compounds, it's crucial to understand the types of extrusion machines available – and what sets the best ones apart.
In this guide, we break down what extrusion machines are and how they work. We’ll explain the differences between single-screw extruders, twin-screw extruders, compounding lines, and sheet extrusion lines. You'll also discover why Useon extrusion machines – known worldwide for their value, reliability, and innovative design – stand out as an ideal choice for businesses looking to upgrade or expand their production.
As the official sales agent for Useon in Australia, New Zealand, and the Pacific Islands, FLEXr Solutions brings these high-performance machines to our region with local expertise and support. Read on to learn how Useon extruders can elevate your manufacturing capabilities, and why partnering with a trusted local supplier like FLEXr Solutions ensures you get a tailored solution that meets your unique needs.
Understanding Polymer Extrusion Machines
Extrusion is a continuous manufacturing process that transforms raw plastic material into finished or semi-finished products. An extrusion machine (or extruder) works by melting plastic pellets, granules, or flakes and forcing the molten polymer through a shaped die.
As the material exits the die, it cools and solidifies in the desired form – whether it's a tube, film, sheet, or plastic pellets for further use. This process is highly efficient for producing consistent, high-volume outputs and is used to make everything from pipes and profiles to sheets and packaging films.
At the heart of every extrusion machine is a screw mechanism housed in a heated barrel. The raw plastic is fed from a hopper at one end of the barrel. As the screw rotates, it pushes the material forward through zones of increasing temperature.
The combined action of heater bands around the barrel and the friction from the screw’s movement melts the plastic. By the time the material reaches the end of the screw, it’s a hot, viscous melt ready to be shaped.
The molten plastic then gets pushed through a die – a metal opening that gives the polymer its new shape. Once through the die, the continuous stream of plastic is cooled (often by air or water or passing through cooling rollers) to harden it into the final product form. This cooling step solidifies the plastic into its intended shape, allowing it to be further handled or processed.
Extrusion machines are favoured by manufacturers for their ability to run continuously and produce long lengths or large quantities of product with uniform cross-sections. They are the workhorses in polymer processing industries, offering a reliable way to make everything from PVC pipes and vinyl siding to plastic films, wire insulation, and wood-plastic composites.
However, not all extrusion machines are the same – different designs exist to handle different materials and processing needs. The most common distinctions are between single-screw and twin-screw extruders, and between standard extruders and specialised systems like compounding extruders or sheet extrusion lines. Choosing the right type of extruder for your application is essential to achieve optimal results in terms of output quality, throughput, and operational efficiency.
Single-Screw Extruders: Simplicity and Efficiency
Single-screw extrusion machines are the most prevalent type of extruder in the plastics industry. As the name implies, they use a single rotating screw inside the barrel to melt and convey plastic. A single-screw extruder is relatively simple in design, which makes it cost-effective, easier to operate, and generally lower in maintenance compared to more complex machines. For many standard extrusion tasks – such as producing pipes, profiles, or standard pellets from a single type of plastic – a single-screw extruder is often sufficient and highly efficient.
How a Single-Screw Extruder Works: The single screw’s helical flight (thread) helps to gradually compress and melt the plastic as it moves along. These extruders typically have zones on the screw: a feeding zone (to intake material), a compression zone (to melt and mix), and a metering zone (to uniformly push out the melt). Because of their straightforward operation, single-screw extruders excel at maintaining a steady output for processes that don’t require extensive mixing or multiple material inputs. They handle a wide range of thermoplastics and are ideal for processes where you feed one main material and simply need to shape it.
Common Applications: Manufacturers often use single-screw extruders for making continuous products like tubing, pipes, profiles (e.g., window frames, weatherstripping), and sheet or film when the material doesn’t require heavy compounding. They are also used in pelletising systems to create uniform plastic pellets from virgin or recycled plastics. If your production involves a single polymer (or a pre-mixed compound) and you need a reliable machine to melt and form it, a single-screw extruder can be a great choice. Its simpler mechanics mean it usually comes at a lower capital cost, and it’s easier to operate for day-to-day production.
However, when your process demands blending of multiple materials, higher levels of mixing, or reactive processing (like adding additives or recycling mixed plastics), that’s where twin-screw extruders shine.
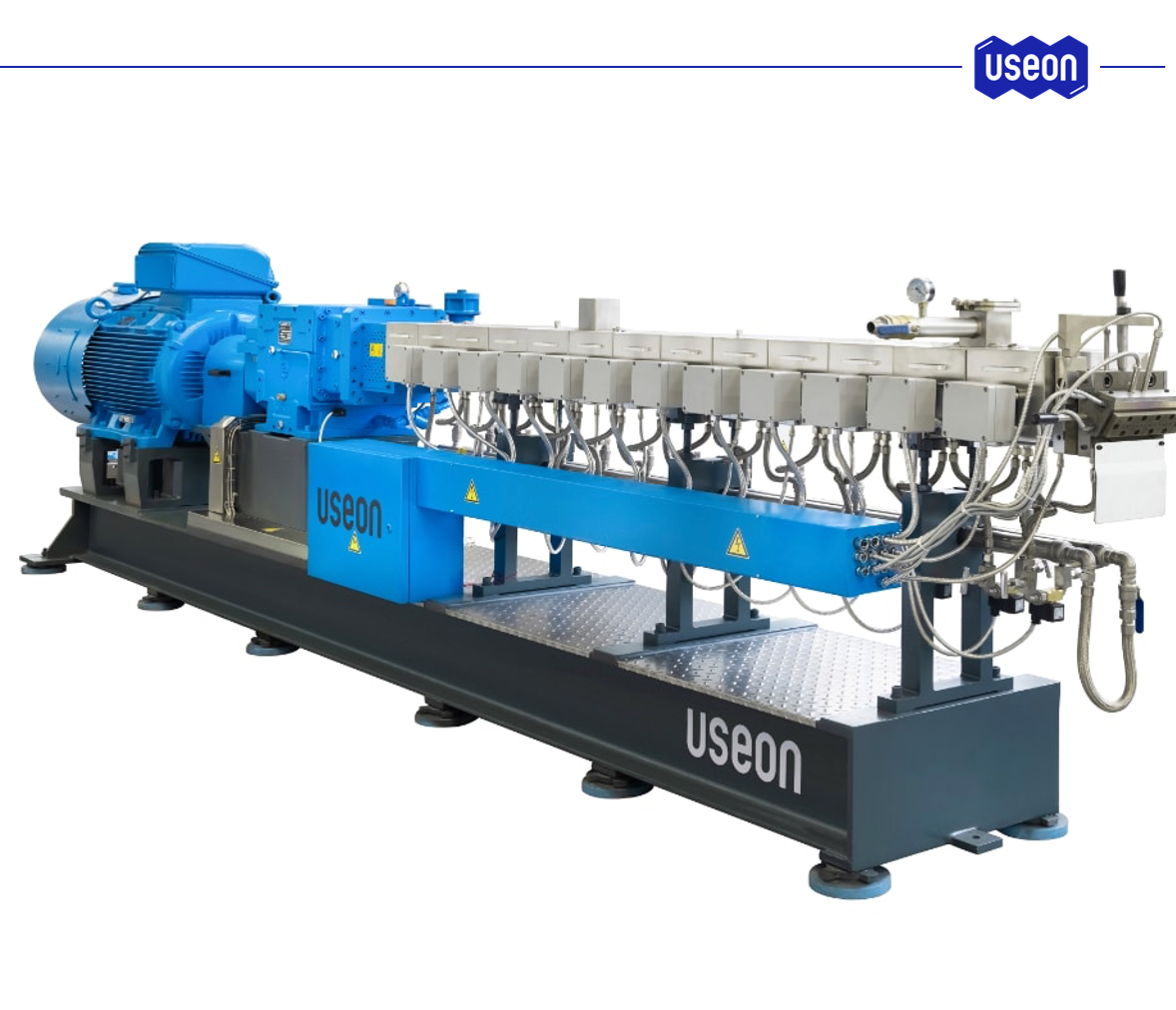
Twin-Screw Extruders: Power and Versatility in Mixing
Twin-screw extruders contain two screws inside the barrel, rotating together to process the plastic. The screws can be configured as co-rotating (turning in the same direction) or counter-rotating, and they can intermesh (their threads overlap) to varying degrees. This twin-screw design brings a new level of capability to the extrusion process, offering superior mixing, compounding, and control over the material behaviour inside the barrel.
Key Advantages of Twin-Screw Extruders
The twin-screw setup is more efficient at mixing and shearing the material, which means additives, fillers, colourants, or even blends of different polymers are distributed more evenly throughout the melt. This is crucial for making high-quality plastic compounds where consistency is important (for example, ensuring a colour masterbatch has uniform pigment dispersion).
Twin-screw extruders also often allow better control of processing because the material can be transferred between the two screws multiple times, improving homogenisation. They can be designed with various segments on the screws (mixing elements, kneading blocks, etc.), allowing customisation of the mixing intensity and residence time to suit specific materials.
Another benefit is that twin-screw extruders generally have better feeding characteristics, especially for powders, flakes, or a mix of materials. The intermeshing twin screws can "grab" and convey materials that might not feed as easily in a single screw.
They also enable processes like venting (removing gases or moisture through vents in the barrel) and reactive extrusion (where a chemical reaction or polymerisation might occur in the extruder) more effectively, because the two screws can continually expose new material to the vent or mix reactants thoroughly.
Twin-screw extruders tend to support higher throughput for certain processes and can often be run at high speeds with high torque, meaning more output without a proportional increase in energy usage – effectively they can be more energy-efficient per kilogram of output when properly optimised.
When to Choose Twin-Screw
If your manufacturing involves combining materials – for instance, blending plastics with fillers like glass fibre or calcium carbonate, mixing in additives for UV resistance or flame retardancy, or recycling plastics with contaminants that need to be filtered and vented – a twin-screw extruder is likely the best fit. These machines are the go-to for compounding tasks (which we’ll discuss next) and any application requiring intensive mixing.
They are common in creating masterbatch (concentrated additive pellets), alloying polymers, or processing plastics that are heat-sensitive (since twin-screw extruders can be configured to reduce shear heat build-up and vent volatiles). While twin-screw extruders are more complex and typically have a higher initial cost than single-screw machines, they deliver versatility and performance that can significantly improve product quality and broaden what you can produce.
In summary, a twin-screw extruder is a powerful workhorse for advanced polymer processing, offering manufacturers in industries such as automotive, packaging, recycled materials, and specialty compounds an efficient solution for challenging jobs.
Compounding Extrusion Lines: Custom Polymer Blends Made Easy
How Compounding Lines Work
When we talk about compounding in the plastics world, we’re referring to the process of mixing together base polymers with various additives and fillers to create a customised material blend, often called a compound. Compounding extrusion lines are specialised systems designed to facilitate this process from start to finish. They typically involve feeding multiple ingredients (plastics, additives, powders, fibers, etc.) into an extruder, thoroughly melting and mixing them, and then pelletising the mixed output into granules that can be reused in manufacturing other products.
A compounding extrusion setup usually centers around a twin-screw extruder, thanks to its superior mixing capability. Upstream of the extruder, there are often gravimetric feeders or hoppers that precisely meter each component (for example, one feeder for the base polymer pellets, others for colour masterbatch, reinforcing fillers, and so on). All these ingredients feed into the extruder’s barrel, where the twin screws blend them into a homogeneous molten compound. Along the barrel, there may be vent ports to remove moisture or trapped air, ensuring the mixture is free of bubbles or volatiles.
Once the mixture is thoroughly melted and mixed, it’s usually pushed through a die at the end of the extruder to form strands, which are then cooled and cut into uniform pellets by a pelletiser (this could be a strand pelletiser with water baths and cutting wheels, or an underwater pelletiser, etc., depending on the material). The end product is a batch of plastic pellets that carry all the combined properties you intended – ready to be molded or extruded again into final products.
Why Compounding Matters
For manufacturers and material suppliers, compounding lines are essential to create materials with specific properties. For example, you might compound polypropylene with wood fiber to make a wood-plastic composite for decking, or add flame retardants and colour to a base polymer to make appliance housings.
Compounding allows incredible flexibility – you can tailor melt flow, strength, colour, weather resistance, and cost by blending different ingredients. If you are a company that needs a custom polymer recipe, having an in-house compounding extrusion line (or using a supplier who runs one) is invaluable. It gives you control over material formulation and quality.
Useon and Compounding
Useon specialises in compounding extruder technology – their twin-screw extruders are at the core of many compounding lines worldwide. These systems are engineered to provide consistent mixing quality and high throughput, which means you get uniform compounds at a production rate that keeps up with industrial demand.
Useon’s compounding lines can handle everything from filling plastics with high levels of calcium carbonate (for cost reduction) to creating masterbatches with precise pigment dispersion. They design their extruders to be versatile, so one line can often be adapted for various formulations. This is particularly useful for businesses that may need to produce different compounds over time – the flexibility is built-in.
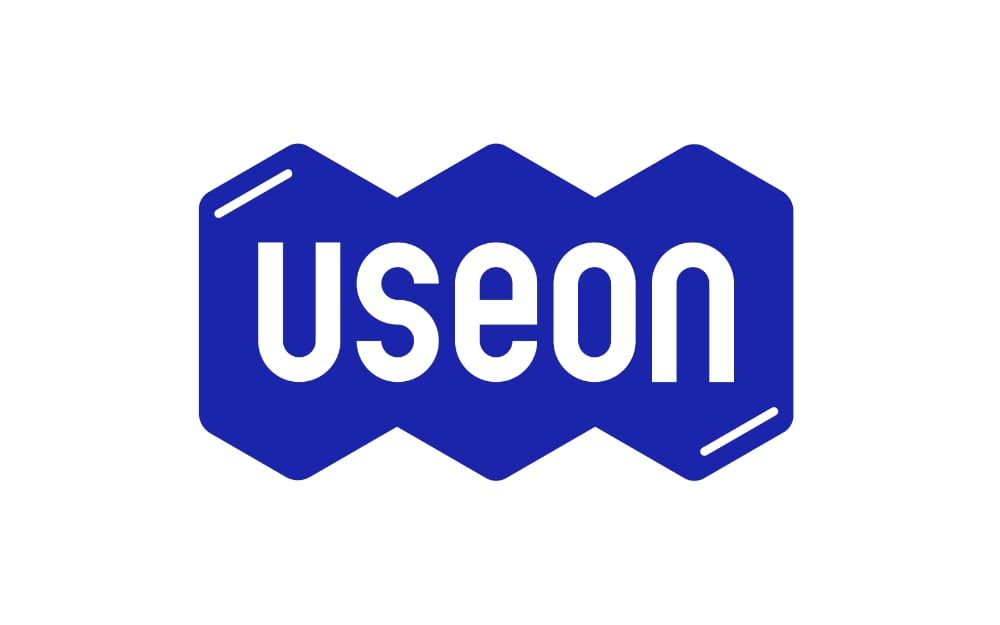
Sheet Extrusion Lines: From Pellets to Plastic Sheets
A sheet extrusion line is a complete production line dedicated to making flat plastic sheets or films through the extrusion process. These sheets can vary in thickness and width and are used in countless applications – think of the clear plastic sheets used for packaging, the glossy sheets for signage, or the thicker sheets of ABS plastic used for thermoformed products like refrigerator liners or vehicle panels.
Unlike a simple extruder that might just produce a shaped profile or pellets, a sheet extrusion line integrates additional downstream equipment to transform the molten polymer into a wide, thin form and ensure it solidifies uniformly.
Components of a Sheet Line
The process starts similarly with an extruder (often a single-screw extruder for a single-material sheet, though multi-layer sheets can use multiple extruders in parallel for co-extrusion). The extruder melts the plastic and pushes it through a flat sheet die, which spreads the molten polymer into a thin, wide curtain. Immediately after the die, the hot, malleable plastic sheet enters a series of calendar rolls (usually a three-roll stack) that press and cool the material to the desired thickness and surface finish.
These rolls are carefully temperature-controlled to cool the sheet gradually and evenly, preventing warping and maintaining clarity or gloss as needed. The gap between the rolls can be adjusted to set the sheet thickness precisely. After the calendering rolls, the continuous sheet passes through additional cooling sections if needed, edge trimming knives (to remove any excess edges or die swell), and then a hauling and winding system that pulls the sheet and rolls it onto large spools (or stacks it as flat sheets).
Key Considerations
Sheet extrusion requires excellent control over thickness and surface quality. Even minor fluctuations in output or temperature can cause variations, so sheet lines often include features like melt pumps (to ensure a consistent, pulse-free flow of polymer to the die) and automatic thickness control systems (such as feedback loops that adjust roll gaps or line speed).
Useon’s sheet extrusion lines, for example, leverage precise control systems to maintain uniform quality, ensuring that the end product meets tight tolerances. Whether you need a thin polypropylene film or a thick polycarbonate board, the principle is the same – achieve a smooth transition from melt to solid sheet without defects.
Applications of Sheet Lines
Businesses in packaging, automotive, construction, and consumer goods all rely on sheet extrusion. If you produce items like blister packaging, plastic trays, clamshells, artificial leather, or thermoformed parts, having your own sheet extrusion line can be a game-changer. It allows you to produce your raw material (the sheet stock) in-house, giving you control over material quality and supply.
Modern sheet lines can also incorporate recycled plastic into the feed, producing sustainable sheets for eco-conscious products. This is yet another area where choosing the right machine makes a difference – a well-designed line can handle a higher percentage of recycled content without compromising on sheet quality.
Why Choose Useon Extrusion Machines?
With a solid understanding of extrusion machine types, it’s clear that investing in the right equipment is a major decision. This is where Useon comes in. Useon is a leading global manufacturer of polymer extrusion machinery, and their extruders are renowned for offering an exceptional balance of performance and value. Here are some of the key benefits that set Useon’s extrusion machines apart:
- Outstanding Value: Useon extrusion machines deliver high-end capabilities at an attractive price point. You get top-tier engineering and results comparable to the world’s leading brands, but with a cost-efficiency that maximises your return on investment. For businesses working within a budget, Useon provides a way to obtain state-of-the-art extrusion technology without overspending. This excellent value has made Useon extruders popular in factories around the world, proving that you don’t have to compromise on quality to save on costs.
- Proven Reliability: When you purchase an extrusion line, reliability and uptime are paramount – any unplanned downtime can be costly. Useon equipment is built for dependable, continuous operation. Their machines feature robust construction and quality components, meaning they can withstand the demands of 24/7 industrial use. Useon has a track record of installations globally, operating successfully in diverse environments and industries. This proven reliability gives manufacturers peace of mind that their production will keep running smoothly year after year. Many users testify that Useon extruders are “workhorses” that require minimal maintenance and provide consistent output.
- Recycling & Sustainability Focus: In today’s world, the ability to handle recycled materials is a big advantage for any extrusion equipment. Useon designs many of its extruders and extrusion lines with recyclers in mind. Whether you want to reprocess scrap plastic into new pellets or incorporate recycled material into your products, Useon machines are up to the task. Twin-screw extruders, for instance, come with venting systems and screw configurations ideal for purging moisture and contaminants often found in reclaimed plastics. Useon also offers specialised lines for PET recycling and even chemical recycling processes. By choosing a Useon extruder, you’re equipping your operation to be part of the circular economy – turning waste plastics into valuable products again. Plus, Useon’s energy-efficient designs help reduce power consumption, aligning with sustainability goals and lowering operating costs.
- Versatility for All Polymer Types: From soft thermoplastics like polyethylene to engineering polymers like ABS or PET – even sensitive bioplastics – Useon extruders can handle them all. The company produces a range of models (single-screw, co-rotating twin-screw, conical twin-screw, even triple-screw and tandem systems) tailored to different materials and processing needs. This means you can likely find a Useon machine suited for your specific application, whether it's producing fine powder for rotational molding, extruding foam sheets, or compounding high-fill materials. Useon’s expertise across various extrusion applications (including foam extrusion, cable compounding, film and sheet production, etc.) ensures that their equipment designs are refined for each task. When you invest in a Useon machine, you get the flexibility to take on new projects and adapt to market changes, because the equipment can often be reconfigured or adjusted to work with different polymers and products.
In short, Useon provides a combination of quality, innovation, and value that is hard to beat in the extrusion machinery market. It’s this blend of benefits that has led FLEXr Solutions to partner with Useon – to bring these advantages directly to manufacturers in our region.
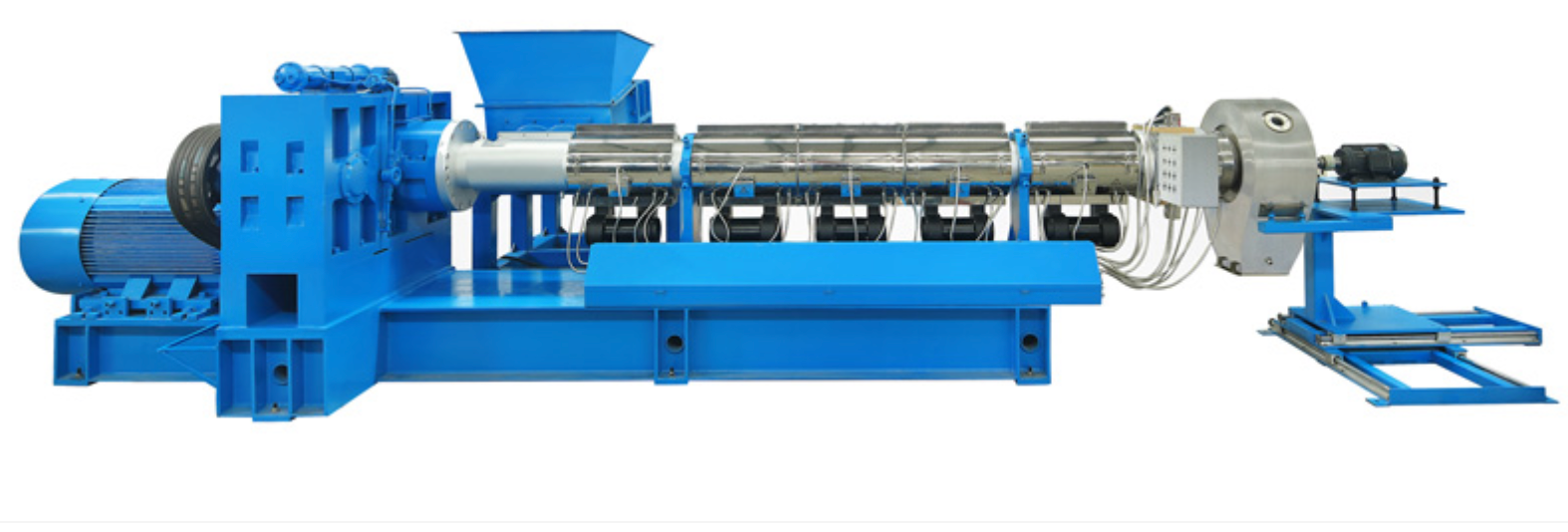
FLEXr Solutions – Your Trusted Local Partner in Australia, New Zealand & the Pacific
Selecting the right extrusion machine is not just about the hardware; it’s also about the support and service behind it. That’s where FLEXr Solutions comes in for businesses in Australia, New Zealand, and the Pacific Islands. As the exclusive regional sales agent for Useon extrusion equipment, FLEXr Solutions offers local expertise to help you make the best investment and keep it running optimally.
Local Expertise and Consultation: Buying complex machinery like an extruder often requires careful consideration of your specific needs – your materials, throughput requirements, space constraints, and future expansion plans. The team at FLEXr Solutions understands the local industry context and is experienced in plastics processing. They will take the time to discuss your production goals and challenges, then recommend the appropriate Useon extrusion solution tailored for you. Whether you’re unsure if you need a single-screw or twin-screw model, or you’re exploring a full compounding line or sheet extrusion setup, FLEXr’s experts can guide you through the options. Their goal is to ensure you get a solution that’s the right fit – technically and financially – for your business.
Seamless Installation and Support: One of the advantages of working with a regional partner is the ease of communication and support. FLEXr Solutions coordinates closely with Useon to handle the procurement, delivery, and installation of your extrusion machine. They help bridge any language or time-zone gaps, so you have a smooth experience from order to commissioning. Once your machine is on-site, the support doesn’t end – FLEXr can assist with training your staff on operation and maintenance best practices. And if any issues arise, you have a local contact who can respond quickly. There’s peace of mind in knowing that expert help is nearby and just a phone call away.
Trust and Reliability: FLEXr Solutions has built a reputation as a trusted supplier by representing some of the world’s leading equipment manufacturers in the rotational molding and recycling industries. By partnering with Useon, they have aligned with a brand that shares a commitment to quality and customer success. For you as a client, this means you’re getting world-class extrusion technology backed by a local company that genuinely cares about your results. FLEXr Solutions is not just selling you a machine – they’re providing a long-term solution and stand by to ensure it continues to deliver value throughout its lifespan.
Encouragement to Act – Find Your Perfect Extrusion Solution: If you’re considering upgrading your production line or venturing into new product areas, now is the time to explore what Useon extrusion machines can do for you. With the combination of Useon’s superior extruder technology and FLEXr Solutions’ regional support, manufacturers in Australia, New Zealand, and the Pacific have a powerful resource at their disposal. Whether it's improving efficiency, incorporating recycling into your process, or increasing your product range, the right extrusion system can make a transformative difference for your business.
Contact FLEXr Solutions today to discuss your needs and discover a tailored extrusion solution for your business. By investing in a Useon extruder through a trusted local partner, you’re setting up your operation for success – with the equipment, expertise, and support to keep you ahead in the competitive manufacturing landscape.